We speak to Dermot Walch, co-founder of Kedel Ltd, a family-owned small company located in the North of England. The company was created in 2010 with the focus on making outdoor furniture for parks, schools and gardens and construction materials entirely out of recycled plastic. Kedel Ltd won the ‘Best Recycled Product’ category at the National Recycling Awards 2015. The products are a great example of the circular economy in action as they can last 50 years or more and can be recycled once again after their initial use.
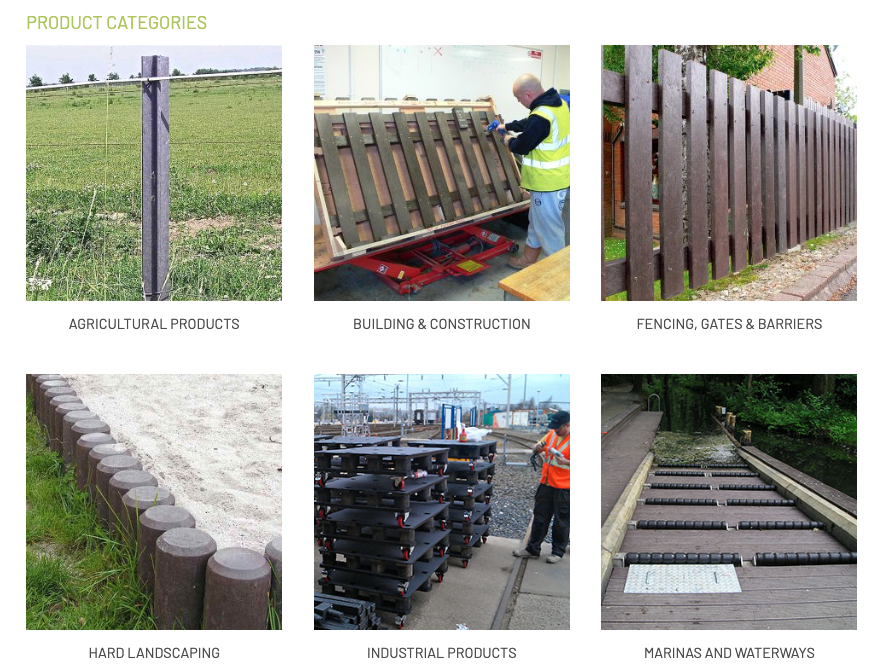
Dermot, what made you start the company?
I started the company with my brother Kieran who did not have a job at that time. During his spare time, he made a compost tumbler for his garden by using an old plastic bin and recycled plastic lumber. Encouraged by his success, he then made some more compost bins in a similar way and sold them on eBay. They sold quite well!
Having been redundant myself at that time and having experience in marketing and sales, I developed a marketing plan and a business plan for recycled products. Then we convinced our eldest brother Lewis, who had worked many years in media, to join us. With our nephews’ help, we created a website and so the business was born. I believe the redundancy was a great push and motivator for us to start our own business.
What were your biggest challenges intially?
No one had any wages and it took some time to make the project profitable. It was difficult to find recycled plastic, there was little to no supply. We bought the machines, but we didn’t have any real knowledge about recycled plastic. We had to learn everything the hard way by making mistakes and it was more difficult than anticipated.
The next challenge was financing, as the costs of machines are quite high. Our initial investment was around £20,000 financed by family and at the beginning we also received a small grant of £2,000. We got our first machine and paid for it monthly. We received another grant for our second cutting and drilling machine. Just to give you an idea of how much the machines cost, our computerised cutting and drilling machine was £70,000. It was difficult at that time, since we had to take a bank loan to cover part of the costs.
Please can you explain how your current business works?
We started working in a 1,000 sq ft facility, a year after we moved to a 6,500 sq ft building and then to a 12,000 sq building. Since 2017 we have been operating from a 14,500 sq ft facility with 3.2 acres of land. In 2021 we had 21 employees in total and our factory works on two shifts of 8 hours.
Since we currently source the recycled plastic from local recycling companies, we only use British sourced waste plastic that reduces our carbon footprint. The plastic is already crashed up and washed, so we put it directly to our machines. It seems that the process to make plastic products is straightforward, as we mix the plastic with calcium carbonate, colour pigment and an ultraviolet stabilizer. However, in practice you always need to be ready for some surprises. For example, the plastic might not melt the right way, or the colour might not be perfect. Therefore, you always need some fine tuning, such as adjusting the temperature, the proportion and always be ready to make changes.
We bought our first machine on eBay and it didn’t work properly. Luckily Kieran managed to rebuild the whole thing so we could use it. We now have four machines, and they are the main costs for our business. Thus, we need to make sure that our machines work well because it takes time to modify and restart them. In the future, we plan to make pellets from the surplus of plastic and sell them locally in the UK.
Currently, we use polystyrene plastic, such as CD cases, contact lens cases and clothes hangers to produce plastic wood planks. We use this plastic to create colourful benches, tables, gates, etc. We also make products from a combination of high and low polyethylene plastic (HDPE and LDPE), such as milk packaging, toys, packaging films, paint trays etc. We don’t use PET plastic because there is something in PET that stops the ultraviolet protection from working.
Normally, we use 20-25 tonnes of plastic per week (1,040-1,300 tonnes per year). We’re very proud that we have never sent any plastic to the landfills; all our offcuts go back into the manufacturing process.
Our customers are mainly based in the UK; however, we also export our products to Australia as they can’t import wood from overseas. Using plastic is a good alternative for them because it is resistant to mould and insects, and it doesn’t rot, crack or splinter.
The good thing about our products is that we don’t need to certify them, which would add delays to our ability to serve our customers. This also allows us to reduce our costs. Our range of products now includes:
- building materials (plastic wood, decking, lumber, etc.);
- fencing and gates;
- landscape materials (raised beds, compost bins, hard landscaping, etc.);
- outdoor products (street, school benches, picnic tables, etc.).
What prevents you from recycling more plastic?
Separating plastic, for sure. There is a lot willingness to recycle waste nowadays, but it is still not compulsory. The UK municipalities are incentivised to recycle waste up to 70% but it is based on the waste weight. So, recycling metal or glass is a lot better than recycling plastic. Unfortunately, all plastic is collected together and sent to the same facility. The waste is still often used for burning, producing energy and the rest goes to landfills instead of being recycled. There are only a few companies that buy plastic waste from the municipalities to wash and crash it so we can then use it to make new products.
Some experts state that you can’t recycle all types of plastic, but experience shows you can, because we are recycling all types. The problem is not the capabilities, but the profitability. Some recycling is not cost efficient. But improving the separating process can improve this. Nowadays, I don’t know many similar companies to Kedel. As a businessman, I value the fact that we don’t have competition but as an environmentalist, I find this heartbreaking. The UK generates roughly 2 million tons of plastic waste, so we need to have more plastic recycling companies.
Are recycled products more expensive?
You need to be looking at the lifetime cost rather than just a short-term cost. Obviously, your wooden decking would be cheaper at first but then on average you need to renew it every 7 years. Whereas you plastic decking, which looks exactly like wood, can last 50 years or more without any maintenance. Recycled products are cheaper in the long run. I have a picnic table in my garden made of recycled plastic since 2010 and it looks like it was put there yesterday.
.png)

Recycled Plastic vs Treated Wood / Timber in Construction of a Walkway
What do you think about the global campaign against plastic pollution?
I don’t see people complaining about milk carton packaging. But sadly, you can’t recycle that type of packaging, it’s all layered. But people still complain about plastic. It’s not what we need. What we need is to completely rethink and change the way we live. We want to reduce our carbon footprint, right? If we make our products of virgin plastic from oil, it will use 2.5 times more carbon than recycled plastic. So, why are we still using virgin plastic? In the world where people talk about being carbon neutral, we need to make more effort and do something serious about it instead of blaming the plastic straws.
If you make it compulsory to use recycled plastic, it will encourage companies to use recycled products more. This will make recycled plastic more comparable to virgin plastic. We need legislation, not just corporate publicity or social media “green experts”. We need to give more power to the Environment Agency and to its Ministry so they can make a real difference.
Can you share any tips for anyone else considering setting up a similar business?
It’s like starting any business. You need to understand that there are lots of setbacks that you will encounter. You need to expect a steep learning curve because plastic can behave differently. What you did yesterday might not work today. We have different videos on our YouTube page on how to work with plastic wood so they might become handy for people starting their own business. Try to find a small commercial niche and understand the market needs in your region and/or country. The quicker you develop your business, the quicker you will start making money. And don’t forget to enjoy the process!
Dermot Walch was interviewed by Aleksandra Sheldukova. This article was sub-edited by